Corvette Fiberglass Molds
There has been a lot of discussion on the internet / web forums about the fiberglass molds which parts are made from. Press mold VS layup, hand lay up VS chopper gun.
Molds: I like to recreate the parts as close to GM style as possible. This means using double sided press molds.
Press mold: means a inner and outer is used and the fiberglass is pressed together much like a waffle iron. In the case of small to medium fiberglass molds both sides are bolted / clamped down on each other till the part is cured. Larger panels like floors / cockpit and nose are in a actual press. In my case a manual press much like Lotus used in the 70’s – 80’s. The size and construction of the mold will differ with the size of the part being made; Lotus cast the full body in 2 pieces. Below is used as an example. This method will have the part with a smooth finish on both sides
Hand layup: These style molds are the most common. This you can find anywhere on the internet or UTube. Sheets of fiberglass or strands are laid in the mold then brushed with resins followed by a roller to level the surface. The exterior of the part is a smooth surface while the inside is a slightly coarse fiberglass. This technique will usually be a little thicker then a press mold
Which is stronger? The press mold is far more ridged , the press clamp method make a stiff structure even with large panels, yet with less actual fiberglass then a hand layup mold. Both are equally as strong, just different techniques
Gelcoat or no gelcoat ? There is really no difference in the structure of the part it self.
Gelcoat helps the problem of broken strands possibly popping out of the structure. It also serves are a much easier base to prime after the work is completed. Setback is gelcoat can crack much easier. Its very popular with aftermarket parts More to come shortly
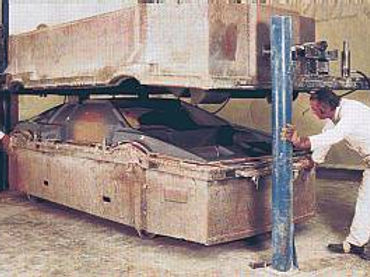
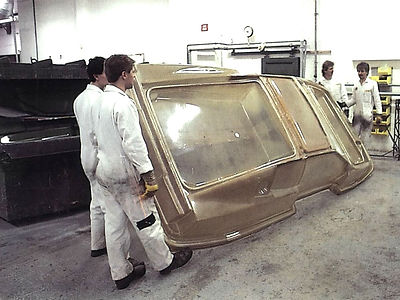